Introduction
Avant de prendre l’apparence que l’on connaît actuellement (pastille de métal), à ses débuts, la monnaie a pu se présenter sous différentes formes et par sa diffusion et sa circulation, elle témoigne aujourd’hui des interactions qui ont pu s’instaurer entre cités, régions et peuples. Objet permettant de calibrer et de faciliter les échanges, elle joue un rôle majeur au sein de ces derniers. Concernant les monnaies en alliages cuivreux, leurs valeurs sont principalement basées sur le système fiduciaire c’est-à-dire que la valeur nominale est supérieure à la valeur métallique. Elle est imposée par l’état et peut circuler grâce à une relation de confiance entre l’émetteur et l’utilisateur (le peuple)1. Dans l’Antiquité, elle se présente sous plusieurs types d’alliages, composés d’or, d’argent ou encore de cuivre (comme le bronze ou le laiton). La grande diversité des monnaies en circulation durant l’Antiquité en ce qui concerne le diamètre, la masse, l’alliage, les types et les légendes, amène à s’interroger sur les savoir-faire et leur transmission, les partages entre populations à des échelles locales comme régionales. Concernant les techniques de fabrication des monnaies en alliages cuivreux, il existe aujourd’hui, pour l’Antiquité, très peu de sources archéologiques et écrites sur celles qui ont pu être employées. Un présupposé de la littérature est l’utilisation de la technique de coulée en chapelet qui pourrait être généralisée à cette époque et qui a pu se diffuser relativement rapidement2. Celle-ci est simple à mettre en œuvre pour l’Antiquité comme peut le montrer l’expérimentation3. Nous verrons à travers cet article de quelle manière il est possible de retracer l’histoire métallurgique des monnaies et comment l’interpréter grâce à leurs microstructures. Les démarches méthodologiques exposées ici apportent des éléments nouveaux à la compréhension de la fabrication monétaire. C’est en associant à la fois les données de composition élémentaires, de microstructure, mais également de dureté qu’il nous est possible d’appréhender les savoir-faire et techniques employés au cours de l’Antiquité. Pour cela, notre corpus d’étude est composé de 135 monnaies en alliages cuivreux (Ve siècle a.C. au IIIe siècle p.C.). Nous verrons aussi selon leurs régions d’émissions quelles peuvent être leurs caractéristiques communes ou non concernant leurs compositions et leurs microstructures.
Matériel et méthode
Échantillons
Le corpus d’étude dont il est question dans cet article se compose de 135 monnaies grecques et romaines en alliages cuivreux. Ces échantillons sont répartis géographiquement de la manière suivante (fig. 1).
Il a été décidé de regrouper leurs régions d’émissions en seulement sept. En effet, certaines étant représentées par une unique monnaie, il a fallu élargir la région étudiée (tab. 1) pour avoir une meilleure représentativité. La définition de ces régions se base sur des regroupements par zones géographiques. On retrouve sur l’histogramme (fig. 2) suivant la répartition chronologique des monnaies.
Nous avons donc ici un corpus étendu en ce qui concerne sa répartition chronologique et géographique. Cette distribution présente des limites, une première étant l’accès aux monnaies pouvant être étudiées de la sorte (détaillée plus bas). Avoir un corpus représentatif à la fois de cette période et de cette vaste localisation nécessiterait d’acquérir beaucoup plus de spécimens. La quantité est ici un facteur limitant puisqu’il faut par la suite préparer les échantillons en suivant toute une série d’étapes (relativement longues) essentielles pour parvenir à leur microstructure. Le temps imparti étant défini par celui de la thèse, il a fallu limiter ce nombre pour laisser la place aux analyses (observations métallographiques, EDXRF, Dureté Vickers, MEB) complétant leur étude. Tout l’intérêt de ce corpus est de pouvoir cartographier les différentes techniques de fabrication qui ont pu être mises en place autour du bassin méditerranéen. Comme expliqué en introduction, très peu de sources écrites et archéologiques sont disponibles sur les procédés utilisés dans l’Antiquité. Cependant, l’objet résultant de cette chaîne opératoire, la monnaie, existe aujourd’hui sous plusieurs formes d’alliages et a été produit en plusieurs exemplaires. Ainsi, pour la reconstituer il est nécessaire d’étudier cet objet final. En effet, tout traitement (thermique et/ou mécanique) qui a pu intervenir va avoir un impact plus ou moins important sur la structure interne du matériau. Certains de ces traitements vont y laisser des traces caractéristiques et c’est en les identifiant et en proposant des interprétations que l’on peut présenter des pistes de reconstitutions des chaînes opératoires de fabrication.
L’étude des échantillons est donc réalisée de la manière suivante. Pour parvenir à la microstructure des échantillons et retracer leur histoire métallurgique, ils ont été découpés. Cela permet de s’affranchir des problèmes de corrosion en surface et d’accéder au cœur sain de la monnaie. Ensuite, ils sont enrobés, polis et une fois ces différentes étapes de préparation terminées ils sont attaqués à l’aide d’un réactif (solution alcoolique de FeCl3) pour révéler leur microstructure. L’étude métallographique est d’abord réalisée par microscopie optique (grâce à un microscope métallographique) puis dans un second temps par microscopie électronique à balayage pour obtenir des informations complémentaires sur la nature et la morphologie des phases, inclusions, impuretés au sein des alliages. Les alliages mis en œuvre par les artisans étant déterminés par spectrométrie de fluorescence X.


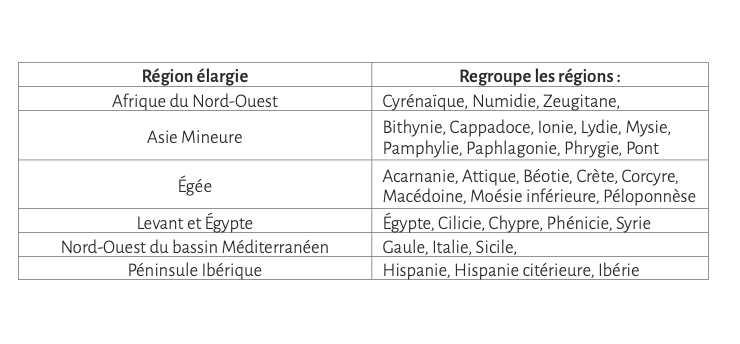
Tableau 1. Description des régions.
Microstructures et métallurgie
Comme expliqué précédemment, les traitements mécaniques et/ou thermiques qui ont pu survenir tout au long de la chaîne opératoire de la monnaie ou d’un autre objet métallique vont avoir un impact sur sa microstructure.
Un traitement mécanique se définit par la déformation (écrouissage) plus ou moins importante du matériau. Dans l’Antiquité, cette déformation peut prendre la forme de martelage, découpe, etc.
Un traitement thermique se réalise à une température et un temps donné. On peut alors en retrouver différents types. Dans l’industrie, un traitement d’homogénéisation se réalise à haute température (fixe) pendant plusieurs heures (3h à 10h) pour réduire la ségrégation chimique (hétérogénéité) du matériau4. Il est peu probable que pour l’Antiquité il ait été mis en œuvre. En effet, cela requiert des temps prolongés qui nécessitent de consommer énormément de combustible. Un autre traitement thermique est le recuit. De manière générale, il est pratiqué après un traitement mécanique. Une fois que le matériau est déformé, il se trouve dans un état durci. Et donc pour restituer sa malléabilité initiale et le rendre plus ductile pour le déformer à nouveau, il est essentiel de réaliser un recuit. Pour les alliages cuivreux, il s’opère dans un intervalle de température de 500°C-800°C5. Dans le cas où il s’effectue après une déformation mécanique, le processus de recristallisation va être activé. Ce processus relativement complexe dépend de plusieurs facteurs (écrouissage préalable, temps et température de recuit, composition, présence ou non d’impuretés et/ou d’inclusions). Au cœur du matériau, la recristallisation est caractérisée par une microstructure présentant des macles et des grains comme le montre la figure 3 (bulles d), e), f)). Il a déjà été présenté que les artisans de l’Antiquité utilisaient ces traitements thermiques et que “le recuit de recristallisation, fait entre 550 et 600°C pendant 6 minutes avec un charbon de bois au rouge naissant et suivi d’une trempe à l’eau améliore considérablement la malléabilité du métal”6. Dans la fabrication monétaire, il a été employé pour rendre le plus de malléabilité possible au matériau avant la frappe et ainsi imprimer plus facilement les types et les légendes7. La trempe est aussi considérée comme un traitement thermique. Elle est réalisée par immersion rapide de l’objet dans un liquide (eau ou huile). L’intérêt, pour les alliages cuivreux, est de pouvoir figer la microstructure dans un état plus malléable et faciliter la déformation du matériau8.
Ainsi à l’aide des explications fournies ci-dessus et la figure 3 il est donc possible à travers la microstructure de l’objet de déterminer si ce dernier a subi un traitement mécanique et/ou un traitement thermique.
En effet, un objet qui n’aura subi aucun traitement mécanique et/ou thermique autre que la coulée aura une microstructure caractéristique dite brut de fonderie. Celle-ci se présente sous la forme a) ou g) avec la présence de dendrites. Tandis qu’un objet qui aura été soumis à un traitement mécanique suivi d’un recuit aura une microstructure dite recristallisée (bulles d), e) et f)). Ainsi, grâce à ces particularités, il nous est possible de pouvoir identifier certaines étapes du processus de fabrication de la monnaie.
Diversité des savoir-faire
Diversité d’alliages
Avant de parler de techniques de fabrication, intéressons-nous d’abord à la nature des alliages mis en œuvre au sein du corpus. Comme le montre la figure 4 et le tableau 2, les résultats de composition élémentaires présentent une grande diversité d’alliage dans les monnaies. Un bronze au plomb est un alliage ternaire constitué majoritairement de cuivre, d’étain et de plomb. Le bronze contient principalement du cuivre et de l’étain tandis que les bronzes mixtes sont des alliages quaternaires composés de divers éléments tels que l’étain, le plomb, le zinc ou de l’argent.
Ces résultats permettent déjà de proposer une variété de fabrication. En effet, si différents alliages ont été fabriqués cela peut être lié à la composition que doit avoir la monnaie. Composition alors régie par l’autorité émettrice9. Dans certains cas, l’utilisation des éléments d’alliages plutôt que d’autres peut également être connectée au contexte économique (pénurie de métaux) et/ou politique (guerres). Ici, l’alliage majoritairement représenté est un bronze au plomb. Étant moins cher que l’étain,10 le plomb va peu à peu le remplacer11 dans les alliages. Nous verrons un peu plus tard comment évoluent ces résultats en fonction des régions d’émissions des monnaies.
Comme le montrent cette figure et la littérature12, différents types d’alliages sont représentés au sein de notre corpus. Selon l’objet que l’artisan souhaite fabriquer, l’alliage n’aura pas la même qualité et les mêmes propriétés mécaniques, suivant sa composition. Concernant les propriétés mécaniques, les solutions solides α obtenues détiennent une grande capacité de déformation à froid. Par exemple un alliage à 8 % d’étain à une résistance mécanique de 250 MPa et un allongement à la rupture de 16 % tandis qu’un bronze au plomb (80 %Cu, 10 %Sn et 10 %Pb) à une résistance mécanique plus faible de 180 MPa et un allongement à la rupture de 7 %13.
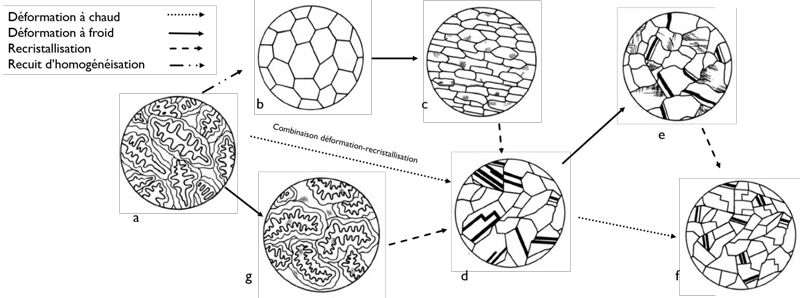
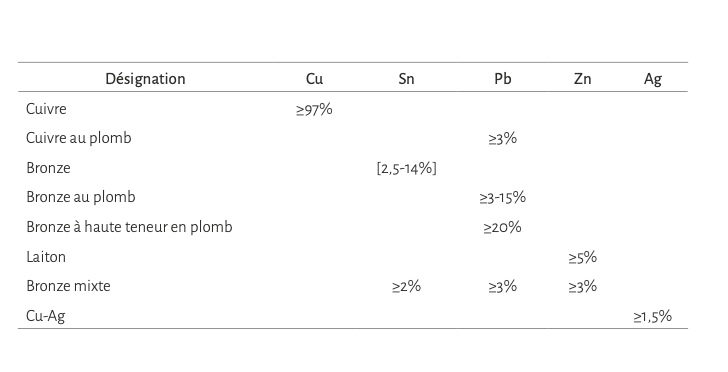
Tableau 2. Définition des alliages identifiés.
Si l’on compare ces données au cuivre pur (résistance mécanique de 200 MPa et limite d’élasticité de 80 MPa) on comprend tout l’intérêt d’ajouter de l’étain pour permettre d’augmenter les propriétés mécaniques de l’alliage et faciliter son travail. Alors que le plomb les dégrade. Pour les laitons ces mêmes phénomènes sont observés, l’ajout de zinc permet d’accroître les propriétés mécaniques des alliages. L’ajout de ces différents éléments d’alliages vient aussi modifier leur couleur. Pour les bronzes à différents pourcentages d’étain, il est alors possible d’obtenir des teintes variées. Pour une teneur inférieure à 5 % il aura une teinte rosée, entre 9 et 15 % des nuances de jaunes et à plus de 20 % il est plutôt blanc14. Ces données peuvent également être mesurées15. Et déjà, Pline l’Ancien décrit certains types de cuivre par leur couleur16. Les laitons auront quant à eux une teinte dorée (entre 10 % et 15 %) et des reflets verdâtres peuvent être obtenus à partir de 30 % de zinc17.
Ainsi, un alliage cuivreux qui doit être soumis à de la déformation doit contenir très peu de plomb et aux alentours de 10 % d’étain, “une pièce coulée, qui ne nécessite pas de déformation plastique, peut être en alliage quelconque, mais une pièce qui doit être battue demande un alliage de qualité exceptionnelle, le plus souvent un alliage binaire, cuivre-arsenic, cuivre-étain, cuivre-zinc, cuivre-argent ou cuivre-or” 18. Un alliage avec des teneurs élevées en plomb sera plutôt destiné à la fabrication d’objets qui nécessitent d’être coulés ou moulés, comme les statues ou certaines parties d’objets qui ne demandent pas de déformation. En effet, l’ajout de plomb permet sous certaines conditions de faciliter la coulée19 et d’abaisser la température de fusion des alliages, mais également de “diluer l’alliage, c’est-à-dire d’augmenter le volume global disponible sans mobiliser davantage de cuivre, d’étain ou de zinc”20 métaux qui pour l’Antiquité ont des coûts plus élevés.
Concernant l’utilisation des alliages on peut voir que cela varie en fonction des régions (fig. 5). En effet, l’Asie Mineure favoriserait l’usage du bronze mixte et du bronze au plomb par rapport à d’autres types d’alliages. L’Égée et l’Afrique du Nord-Ouest (égalité avec le cuivre au plomb) auraient un emploi majoritaire du bronze. Pour la Péninsule Ibérique et le Nord-Ouest du bassin méditerranéen, c’est le bronze au plomb qui est alors préféré.
Pour cette dernière, le pourcentage en plomb des échantillons ne dépasse pas 25 % (fig. 6), tandis que pour la région Levant et Égypte les monnaies peuvent atteindre des teneurs supérieures à 30 % pour un maximum à plus de 40 % (fig. 6). Concernant les autres régions, peu d’échantillons (seulement deux, un en Afrique du Nord-Ouest et un autre en Égée) franchissent une teneur en plomb de 30 % (fig. 6). L’utilisation du plomb à haute teneur est, ici, assez caractéristique de la région Levant et Égypte. Même si ces régions montrent un emploi prédominant d’un alliage spécifique, chacune illustre l’usage plus ou moins prononcé de ces différents alliages.
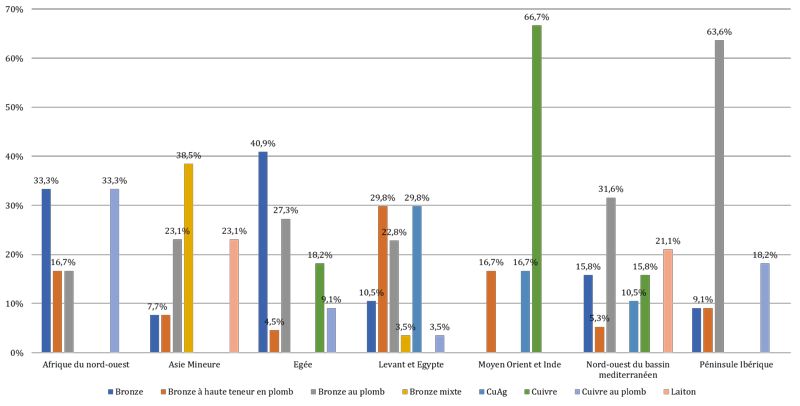
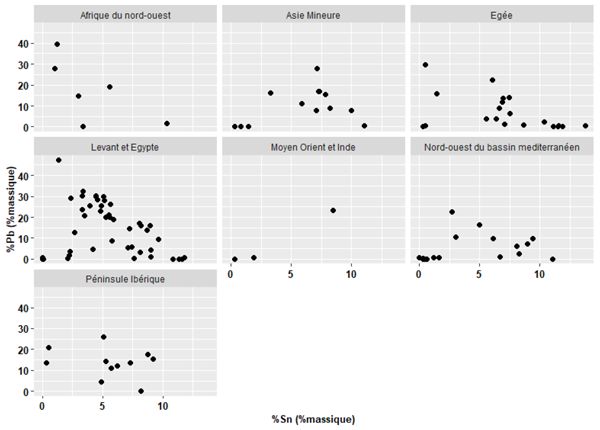
Diversité de microstructures
Si l’on s’intéresse maintenant plus particulièrement aux microstructures qui composent nos monnaies, différents groupes se distinguent au sein de notre corpus comme le présente la figure 7.
La figure suivante montre les microstructures caractéristiques à chacun des groupes (fig. 8). Le plus important (67 %, fig. 7) est constitué d’échantillons recristallisés et d’échantillons présentant des signes de recristallisation. Comme le présente la figure 8 et la micrographie caractéristique de ce groupe (Fig. 8 (a)) c’est une microstructure constituée de grains et de macles dite recristallisée. Cette recristallisation est la conséquence d’un traitement mécanique suivi d’un recuit. Celui-ci a pour but de rendre plus malléable le métal et réduire les contraintes au sein du matériau.
Ces différents éléments mettent donc en avant des étapes supplémentaires de la chaîne opératoire ou bien des procédés de fabrication plus complexes avec plus d’étapes (traitements mécaniques, recuits), mais également plus d’opérateurs et nécessitant plusieurs installations (four de fonte des alliages, four de recuits).
Le présupposé de départ suggère l’emploi de la technique de coulée en chapelet, car pour l’Antiquité c’est une méthode simple à mettre en œuvre et à utiliser 21. Et qui a démontré ses preuves par l’expérimentation22 et pourrait expliquer un usage et une diffusion relativement répandus pour le bassin méditerranéen. Mais au regard des microstructures recristallisées prédominantes mises au jour pour les monnaies en alliages cuivreux, à travers ce corpus, il paraît peu probable que l’utilisation de cette technique soit prédominante. Concernant les microstructures granulaires, ces dernières peuvent soit résulter d’un recuit préalable à la frappe23 ou d’un refroidissement lent en moule après avoir été coulées conduisant à ces particularités24. Pour le groupe intermédiaire, il avait, au départ, été créé, car il était difficile de classer ces échantillons dans un groupe plutôt qu’un autre.

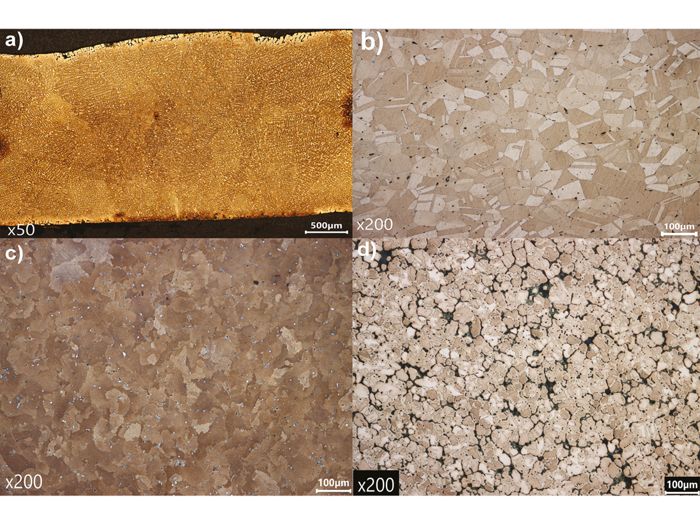
Les différents éléments présentés dans la partie précédente laisseraient suggérer que des monnaies constituées de bronze au plomb ou de bronze à haute teneur en plomb auraient été moulées. En effet, une tendance est mise en avant ici (fig. 9), celles composées des alliages comme le cuivre au plomb et le bronze à haute teneur en plomb ont pour une majorité des microstructures brut de fonderie. Elles n’auraient donc subi aucun traitement mécanique et thermique mis à part peut-être la frappe monétaire pour certaines. Pour les alliages de bronze, de cuivre-argent, de laiton ou des monnaies en cuivre, les échantillons ont une majorité de microstructures recristallisées. Ces monnaies constituées d’alliages de bonne qualité ont ainsi été soumises à des traitements mécaniques suivis de traitements thermiques au sein de leur processus de fabrication.
Si l’on regarde la distribution des échantillons selon leurs microstructures en fonction des différentes régions ici représentées (fig. 10) le plus grand nombre sont recristallisés, peu importe leur région d’origine. Cependant concernant ceux provenant d’Afrique du Nord-Ouest, d’Asie Mineure ou encore Levant et Égypte, une partie non négligeable détiennent des microstructures types brut de fonderie. Au sein d’une même région, plusieurs techniques semblent avoir été adoptées et mises en œuvre. Il est également très probable que techniques, savoir-faire et styles iconographiques ont pu circuler suivant les fluctuations géopolitiques25, notamment à travers l’installation d’ateliers itinérants26, mobiles en fonction des guerres27 et à l’aide des soldats28.

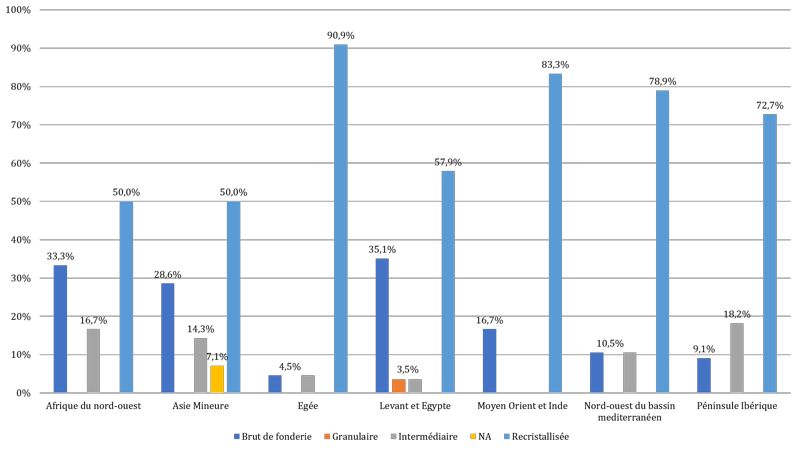
Conclusion
La monnaie, objet qui permet de calibrer et de faciliter les échanges entre régions et peuples, joue un rôle majeur dans les échanges. Nous avons vu à travers cette étude qu’avec la diversité de formes qu’a pu prendre la monnaie (alliages d’or, d’argent ou de cuivre), les alliages cuivreux présentent également une diversité. En effet, différents alliages cuivreux (cuivre, cuivre au plomb, bronze, bronze au plomb, bronze à haute teneur en plomb, bronze mixte, cuivre-argent, laiton) se retrouvent au sein des monnaies de notre corpus. En dépit des limites connues que présente ces exemplaires, une variété de processus de fabrication de la monnaie sont ici mis en avant. Les microstructures des échantillons suggèrent l’emploi de techniques simples (coulée en chapelet, monnaies moulées) ou des techniques plus complexes, mettant alors en jeu des étapes supplémentaires de traitements mécaniques et thermiques au sein de la chaîne opératoire. Ainsi, si l’on s’intéresse à comparer ces diversités entre les différentes régions d’émissions des monnaies des tendances montrent que certaines régions ont préféré l’utilisation de certains types d’alliages plutôt que d’autres (par exemple la région Levant et Égypte avec le bronze à haute teneur en plomb). Même si ces régions montrent un emploi prédominant d’un alliage spécifique, chacune illustre l’usage plus ou moins prononcé des différents alliages identifiés. Il serait intéressant dans le futur de réaliser des comparatifs avec d’autres types d’objets étant issus de ces régions, permettant ainsi d’étudier si les évolutions de composition en fonction des années d’émissions des monnaies et des années de fabrication des objets sont vérifiées et de pouvoir les comparer à plus grande échelle. L’étude de l’approvisionnement de leurs stocks métalliques pourrait nous indiquer si ces différentes régions s’approvisionnent en minerais au même endroit par exemple. Dans l’ensemble, elles présentent en majeure partie des monnaies avec une microstructure recristallisée (ayant donc mis en jeu des étapes plus complexes) même si pour les régions Afrique du Nord-Ouest, Asie Mineure ou encore Levant et Égypte une partie non négligeable des monnaies issues de ces régions détiennent des microstructures types brut de fonderie. L’analyse de réseaux comme présentée par Daniel Da Silva Pereira lors de cette Journée des Doctorant.es dans sa communication intitulée “Network Analysis Applied to the Spread of Symbolic productions during the Early Neolithic in Western Mediterranean” pourrait également permettre d’approfondir ces pistes de recherches et ces questionnements sur les échanges monétaires et savoir-faire. Une autre manière de pouvoir étudier les échanges entre régions serait aussi de s’intéresser aux problématiques iconographiques.
Remerciements et contributeurs
Plusieurs personnes ont contribué à la réalisation de cet article :
Thomas Faucher (Centre d’Etudes Alexandrines – UASR 3134 CNRS) et Florian Téreygeol (UMR 7065 IRAMAT) pour leurs conseils. Yannick Lefrais (Archéosciences Bordeaux, UMR 6034) pour son aide et ses conseils pour les mesures EDXRF, MEB-EDX et la maintenance du matériel. Les résultats présentés s’inscrivent dans le cadre d’une recherche doctorale menée au sein du laboratoire Archéosciences Bordeaux, auquel j’appartiens et regroupe également les travaux de trois étudiants de Master (Tobias Heal, Lucie Pichon et Clarence Pambu) et d’un étudiant de l’Institut Technologique de Bordeaux, Maël Gancel (IUT de Bordeaux et laboratoire I2M). Ce contrat de recherche est réalisé dans le cadre du projet “Frapper Monnaie”, dirigé par le Dr. Thomas Faucher et financé par l’Université Bordeaux Montaigne et la Région Nouvelle-Aquitaine.
Bibliographie
- Amandry, M., dir. (2017) : La monnaie antique : Grèce et Rome, VIIe siècle av. J.-C.-Ve siècle apr. J.-C, Le Monde, une histoire, Mondes anciens, Paris.
- Amandry, M. et Dhénin, M., dir. (2001) : Dictionnaire de numismatique, Paris.
- Arnaud, D., Barbery, J., Biais, R., Fargette, B. et Naudot, P. (1985) : “Propriétés du cuivre et de ses alliages”, Techniques de l’ingénieur, 52.
- Barbery, J. (1991) : “Traitements thermiques du cuivre et de ses alliages”, Techniques de l’ingénieur, 23.
- Barralis, J. et Maeder, G. [1997] (2005) : Métallurgie : Élaboration, structures-propriétés, normalisation, Précis, Paris.
- Blet-Lemarquand, M. (2013), “Les analyses élémentaires de monnaies de bronze grecques réalisées au Centre Ernest-Babelon de l’IRAMAT : méthode, résultats, synthèse”, in : Grandjean et Moustaka, éd. 2013, 39‑56.
- Blet-Lemarquand, M. (2019). “How the Greeks manipulated the composition of their bronze coins. Case studies”, in : Baas, P., éd. : Proceedings of the XXth International Congress on Ancient Bronzes, 145-153, Oxford.
- Blondé, F., dir. (2016) : L’artisanat en Grèce ancienne : Filières de production : bilans, méthodes et perspectives, Archaologia, Villeneuve d’Ascq.
- Bost, J.-P. (2019) : “Routes, cités et ateliers monétaires : Quelques remarques sur les officines hispaniques entre les règnes d’Auguste et de Caligula”, in : Bost, J.-P. éd. : L’Empire romain et les sociétés provinciales, Ausonius Scripta Antiqua 22, 433‑456, Pessac.
- Caley, E. R. (1939) : “The Composition of Ancient Greek Bronze Coins”, Memoirs of the American Philosophical Society, 11.
- Craddock, P.T. (1976) : “The Composition of the Copper Alloys used by the Greek, Etruscan and Roman Civilizations 1. The Greeks before the archaic period”, Journal of Archaeological Science, 3, 2, 93‑113.
- Craddock, P.T. (1977) : “The composition of the copper alloys used by the Greek, Etruscan and Roman Civilisations 2. The Archaic, Classical and Hellenistic Greeks”, Journal of Archaeological Science, 4, 2, 103‑123.
- Davis, J.R. (2001) : Copper and copper alloys, ASM specialty handbook, Ohio.
- Dungworth D. (2013) : “An experimental study of some early copper smithing techniques”, in : Dungworth, D. et C. P. Doonan, R., éd. : Accidental and Experimental Archaeometallurgy, 149–152, Londres.
- Duyrat F. (2014) : “Les étalons monétaires grecs : une introduction”, Dialogues d’histoire ancienne, 12, 1, 103-123.
- Faucher, T. (2013) : Frapper monnaie : la fabrication des monnaies de bronze à Alexandrie sous les Ptolémées, Alexandrie.
- Faucher, T., Téreygeol, F., Brousseau, L., et Arles, A. (2009) : “À la recherche des ateliers monétaires grecs : L’apport de l’expérimentation”, Revue Numismatique, 6, 165, 43–80.
- Flament, C. (2010) : Contribution à l’étude des ateliers monétaires grecs : étude comparée des conditions de fabrication de la monnaie à Athènes, dans le Péloponnèse et dans le royaume de Macédoine à l’époque classique, Louvain-la-Neuve.
- Fournier, É. (2002) : “Les Origines D’un Atelier Monétaire Itinérant : Réflexions à Partir Des Cas De Trèves, Milan et Sirmium (IIIe–Ve siècles)”, Mouseion: Journal of the Classical Association of Canada, 2, 2, 245‑261.
- Grandjean, C. et Moustaka, A. (2013) : Aux origines de la monnaie fiduciaire : traditions métallurgiques et innovations numismatiques actes de l’Atelier international des 16 et 17 novembre 2012 à Tours, Ausonius Scripta antiqua 55, Pessac.
- Hill, G.F. (1922) : “Ancient methods of coining”, The Numismatic Chronicle and Journal of the Royal Numismatic Society, 2, 1‑42.
- Howgego, C. (2005) : The Antonines (AD 138–192): Egypt, Roman Provincial Coinage, IV, 4, Oxford.
- Mattingly, H., Sutherland, C. H. V., Carson, R. A. G., éd. (1986) : Pertinax – Uranius Antonius, The Roman Imperial Coinage, IV Londres
- Mc Alee, R. (2007) : The coins of Roman Antioch, Lancaster, PA.
- Meadows, A. R. et Bagwell-Purefoy, P. (2002) : Sylloge Nummorum Graecorum – IX: The British Museum, 2, Spain.
- Mecking, O. (2020) : “The colours of archaeological copper alloys in binary and ternary copper alloys with varying amounts of Pb, Sn and Zn”, Journal of Archaeological Science, 121, 105199.
- Pernot, M., dir. (2017) : Quatre mille ans d’histoire du cuivre : fragments d’une suite de rebonds, Pessac.
- Schmitt, S., éd. (2013) : Pline l’Ancien, Histoire naturelle, Bibliothèque de la Pléiade, Paris.
- Scott, D.A. (1991) : Metallography and microstructure of ancient and historic metals, Californie.
- Toledo i Mur, A., Pernot, M., Adamski, F., Benquet, L., Fluzin, P., Hiernard, J., Orengo, L., Poirier, P., O’Farrell, M. et Odenhardt-Donvez, I. (2008) : “Un atelier monétaire gaulois près de Poitiers : les Rochereaux à Migné-Auxances (Vienne)”, Gallia, 65, 1, 231‑272.
- Wickham, H. (2016) : ggplot2: Elegant Graphics for Data Analysis. Springer-Verlag, New York.
Notes
- Grandjean et al. 2013 ; Duyrat 2014.
- Amandry, dir. 2017.
- Faucher et al. 2009.
- Davis 2001.
- Arnaud et al. 1985 ; Barbery 1991 ; Davis 2001 ; Dungworth 2013 ; Pernot 2017, dir.
- Pernot 2017, dir., 284.
- Toledo i Mur et al. 2008.
- Barbery 1991 ; Pernot 2017, 70.
- Blondé 2016 ; Amandry, dir. 2017 ; Blet-Lemarquand 2019.
- Plin., HN, 34 ; Blet-Lemarquand 2019.
- Caley 1939 ; Craddock 1976 ; Craddock 1977.
- Craddock 1976 ; Craddock 1977 ; Blet-Lemarquand, éd. 2013 ; Pernot, dir., 2017 ; Blet-Lemarquand 2019.
- Arnaud et al. 1985 ; Davis 2001 ; Barralis et al. 2005.
- Blet-Lemarquand, éd. 2013 ; Pernot, dir., 2017.
- Mecking 2020.
- Plin., HN, 34.1549‑1570.
- Arnaud et al. 1985, 8.
- Pernot 2017, dir., 277‑290.
- Mille 2017.
- Mille 2017, 375.
- Hill 1922 ; Amandry, dir. 2017.
- Faucher et al. 2009.
- Toledo i Mur et al. 2008 ; Pernot 2017, dir., 53.
- Faucher 2013.
- Flament 2010.
- Amandry, dir. 2017, 11, 272 ; Amandry 2001, 37, 503.
- Fournier 2002.
- Bost 2019.